The Washington Post did the nation a service last week by recognizing that the near death of one relatively famous worker had received far more attention than the millions of workers endangered by far more serious hazards faced on a daily basis across the United States. That worker, Damar Hamlin, was employed in the sports industry — specifically a dangerous occupation known as “football” where their working conditions involve being violently assaulted on a regular basis, often resulting in broken bones, life-threatening concussions and, in Hamlin’s case, heart problems. (Not too dissimilar to the working conditions of health care and social service workers.)
The fact that some worker deaths and injuries receive more attention than others is not a new concept. In 2003, I wrote an article called Acts of God; Acts of Man where I similarly compared the attention paid to seven astronauts (aka space workers) who were killed in the Columbia space shuttle, to workers who fall off scaffolds and die in trenches every day. (Read it. It still stands up pretty well after 20 years, even if I do say so myself.)
Over 100 workers die in fatal workplace incidents each week, and several times that number die each week from occupational disease. Millions face serious work-related injuries each year. Almost all of those deaths and injuries go un-noticed and unrecognized, except by family members, friends, coworkers and those who bother to read about the few incidents that are recounted in the local media. The media tends to prefer workplace incidents where the victims are well known, where a lot of workers get killed or the death is fairly gruesome. Most worker deaths don’t make the news at all.
The media tends to prefer workplace incidents where the victims are well known, where a lot of workers get killed or the death is fairly gruesome.
Most who work in dangerous jobs don’t make as much money or are as well known as Hamlin. The Post quoted Tonya Ford, whose uncle was killed in a grain facility and who until recently directed United Support and Memorial for Workplace Fatalities, a nonprofit that helps families and communities after occupational deaths. They also quoted Jessica Martinez, co-executive director at the National Council for Occupational Safety and Health, Mine Workers president Cecil Robert and other worker advocates. All spoke of the hazards that many workers face every day, often in low-paying jobs, the difficulty they encounter trying to correct the hazards, and the retaliation they face when they complain of hazards or report injuries.
“Every day, the average person who walks into some of these essential jobs is putting themselves in danger, and they’re aware of it. But they’re not making professional sports wages,” said Marie Watson, a mechanic at Mission Foods’s factory in Pueblo, Colo., and a steward for the local United Food and Commercial Workers union. She has memories of ambulances pulling up to her factory to treat colleagues experiencing heat illness.
“And a lot of people may argue, ‘Once a week, [NFL players are] putting themselves up to be in a car crash,’” Watson added. “Right: once a week. How about those folks that go in every day?”
Don’t Blame Workers
So far so good. But then the Post descends into dangerous territory
But accidents and injuries on many job sites are inevitable, experts concede. That’s why it’s crucial to help employees manage their well-being and mind-set, said Cindy DePrater, chief environmental health and safety officer at Turner Construction, which operates 1,500 construction sites, through which about 100,000 workers pass, each year.
“There’s really four things that get people hurt: rushing, frustration, fatigue or complacency,” DePrater said.
Now Turner is one of the better companies in the construction industry. They always participated in and co-sponsored OSHA’s annual construction safety stand downs, and I worked with Cindy on those.
So what’s wrong with these statements?
Everything.
First, what’s the problem with believing in the inevitability of workplace injuries. As I wrote twenty years ago, “If workplace deaths are inevitable, if there is nothing anyone can do about them, then the employer has limited responsibility for workplace deaths and injuries, and the government has no useful role in issuing or enforcing workplace standards.”
But worse, DePrater’s statement is based on a disproven theory called “behavior-based safety” — more commonly known as “blame the worker.” According to this theory, most workplace injuries and “accidents” are the result of unsafe acts by workers. Workers get hurt and killed because they are careless, not paying attention, rushing, goofing off, or just “complacent” — they just don’t care if they or their co-workers get injured. In other words, it’s their fault they got injured. If only they had behaved more safely everything would have been fine. (You can read much more about blaming the worker here.)
The United Steelworkers union has done in-depth studies of behavior-based safety and the real causes of workplace injuries and deaths: “What we almost always find when we investigate catastrophic accidents including fatalities is that multiple root causes that are related to hazards and unsafe conditions, not multiple unsafe behaviors, cause the accident.”
“What we almost always find when we investigate catastrophic accidents including fatalities is that multiple root causes that are related to hazards and unsafe conditions, not multiple unsafe behaviors, cause the accident.” — United Steelworkers
Part of the problem is that behavioralists are only looking at the direct causes of incidents, not the root causes. Root cause analysis of any incident demands that you keep asking “why” until you get to a “root cause” that can be changed to prevent all similar incidents.
For example, maybe you have determined that a worker got injured because he was “rushing.” But that’s not the end of the investigation; it’s the beginning. You then need to ask why he was rushing. Is it because of an unreasonable deadline? Quotas? Understaffing? Are there conditions not under a worker’s control that my force him or her to “rush?”
The problem with stopping at the most superficial cause is that you can educate the worker about the hazards of rushing, or even fire him or her — but if the underlying root causes (e.g. unreasonable deadlines or understaffing) remain, the problem isn’t resolved. Another worker will soon get injured by “rushing.”
How about “frustration.” If equipment isn’t working properly or procedures are outdated, it may cause “frustration.” Strenuous work, late hours, mandatory overtime, shift work and low pay (and the need for a second job) may cause “fatigue.”
“Complacency” always gets me. When I was working for a union, a high-level OSHA official once explained to me that the solution to back injuries and musculoskeletal disorders was to just educate workers and make them realize that lifting objects that were too heavy, or not being “careful” about how they do their work, could impact their health and the wellbeing of their families.
Aside from the assumption that workers somehow don’t realize that serious injuries can negatively affect their lives, there is no realization that their jobs often require lifting heavy objects.
Among the many root causes identified by the Steelworkers are equipment not available, faulty equipment, quotas, known hazards not corrected, lack of training, missing or faulty safety devices, lack of maintenance, process and equipment design and many others.
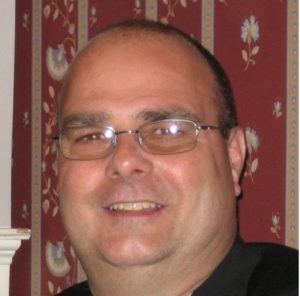
Comprehensive Workplace Safety and Health Programs are the answer
And the problem is that when behavior-based safety moves in, it crowds out the need for a comprehensive workplace safety and health programs that emphasize worker (and union) participation, identification of workplace hazards and unsafe conditions, and the use of the hierarchy of controls (elimination of the hazard, engineering controls, administrative controls and finally Personal Protective Equipment).
Jonathan Karmel, author of Dying to Work, which contains powerful human stories of workplace deaths, injuries and illnesses, points out that every incident he wrote about in that book was preventable. He uses the death of Tonya Ford’s uncle, recounted in the Post, as an example of how far off DePrater’s causes of death are:
Tonya Ford’s uncle, Bobby Fitch, didn’t fall to his death from a manlift inside a grain elevator owned and operated by Archer Daniels Midland due to an accident. The manlift did not have a guard on it that would have prevented Bobby Fitch falling to his death. It wasn’t an unknown or unforeseeable event. ADM knew the manlift was unsafe, but it was permitted not to eliminate the hazard required by regulation because this manlift was “grandfathered” from regulatory compliance. In other words, ADM’s bottom line was more important than eliminating a known workplace hazard. The only thing inevitable at this ADM grain elevator is that some worker would fall resulting in their horrific death or injury.
Management often objects to OSHA citations because, they claim, workers refused to use safety equipment or were engaged in “unavoidable employee misconduct.” But those excuses almost never work once the facts are known.
While I was at OSHA, one employer passed out fall protection equipment to workers after a worker had fallen to his death, and then claimed the dead worker had been on his cell phone when he fell off the roof. In other cases, employers claim that unbeknownst to management, a worker died after disabling the safety locks to repair a machine that was in operation. Later, video showed that managers routinely ordered workers to bypass the safety mechanism.
(Legal note to employers who might be tempted to lie to OSHA inspectors: Penalties are much higher for lying to a government official than for killing a worker.)
Conclusion: Protect Workers, Don’t Blame Them
Most workplace injuries and deaths are caused by unsafe conditions, not unsafe behaviors. Workers need to make sure that incidents are thoroughly investigated — down to the root causes. Keep asking “why”. And then make sure those unsafe conditions are corrected — preferably before someone is injured or killed.
Also, challenge reporters who fail to question the superficial causes pushed by managers. Reporters generally aren’t safety and health experts. You are. You need to educate them. You need to urge them to dig deeper. Call them. Email them. (For example, this post will be sent to the Washington Post reporters who wrote the story.) Sometimes, you’ll even succeed in getting reporters to follow-up on a story.
Finally, of course, every workplace needs a union. For a variety of reason, but especially because a union is generally the best way to protect workers’ safety and health.
THIS!!!
From Monona Rossol, President/founder of Arts, Crafts and Theater Safety, Inc:
Why aren’t we using this kind of a statement to help all readers and workers understand that OSHA doesn’t cite workers for rushing, frustration, fatigue or complacency (about following safety rules). If there is an accident caused by rushing, frustration, fatigue or complacency, the employer gets the OSHA citation. And rightly so.
The regulations are clear: the employer is supposed to have work schedules that don’t require rushing, result in fatigue, and incite frustration. If workers are not getting enough time to do the work safety, that is NOT the worker’s fault. It is the employer’s fault.
In addition, employers are required to have an accident prevention program that provides worker training about these issues PLUS an internal enforcement policy which would prohibit workers from being complacent and deciding to take these risks.
The worker is not in control of schedules and conditions in the workplace, the employer is.
So whenever rushing, frustration, fatigue and complacency are cited as causes in an attempt to blame worker, all readers need to correctly interpret this as good evidence that the employer is not doing right by the workers on this location.